Dustless Sandblasting: How Does It Actually Work?
In the modern stonemasonry workshop, managing dust is a significant concern for both health and cleanliness. Dustless sandblasting technology offers a compelling solution. But how does it achieve this cleaner, safer operation? In essence, a dustless sandblaster, like those from Sandblast Tech, ingeniously combines the power of a conventional sandblaster with an integrated vacuum system and a sophisticated multi-stage filtration process.
The Blasting Head – The Heart of the System
The magic begins at the point of application. The sandblasting nozzle is encased within a specialised brush head. This head, when pressed against the workpiece, creates a seal, functioning much like a vacuum attachment. Imagine an inverted smoking pipe: the abrasive delivery hose connects to one part of this head (akin to the ‘bowl’ of the pipe), while a suction hose is attached to another (the ‘stem’).
The Process – From Impact to Immediate Recovery
During operation, abrasive media is propelled from the nozzle, striking the stone surface. This impact dislodges surface material and simultaneously causes some attrition of the abrasive itself. The crucial difference is that this mixture of spent abrasive, stone particles, and resultant dust is immediately drawn away from the work surface into the sandblaster’s closed-circulation system.
The Three-Stage Separation System – Reclaiming Your Abrasive
This is where the ingenious process of separating reusable abrasive from waste dust begins, typically in three distinct stages:
Stage I: Primary (Gravity) Separation
As the vacuumed mixture enters the upper feed hopper of the machine, the heaviest particles – the reusable abrasive – fall directly to the bottom due to gravity. This is achieved through an optimal balance of the suction motor’s power, the design of the tanks and dust collection box, filters and the nozzle configuration. This careful engineering ensures that valuable abrasive isn’t lost by being drawn into subsequent filtration stages.
Stage II: Cyclone Filtration
The remaining lighter mixture of dust and finer particles then passes into a cyclone filter (often visible as a tall tube on the side of the sandblaster, typically with a collection bin at its base). Here, centrifugal force separates heavier dust particles, which are then deposited into this dedicated collection bin.
Stage III: Final Filtration & Dust Collection
The very finest, lightest dust, which bypasses the cyclone, is captured in the third stage by a high-efficiency industrial cylindrical filter housed within the main dust box (often a prominent, coloured enclosure). This residual dust settles into a special collection drawer for easy disposal. The filter itself is kept clean by an automatic dual-cleaning system, employing both a pneumatic pulse (a sharp blast of air) and mechanical vibration to dislodge particulate matter.
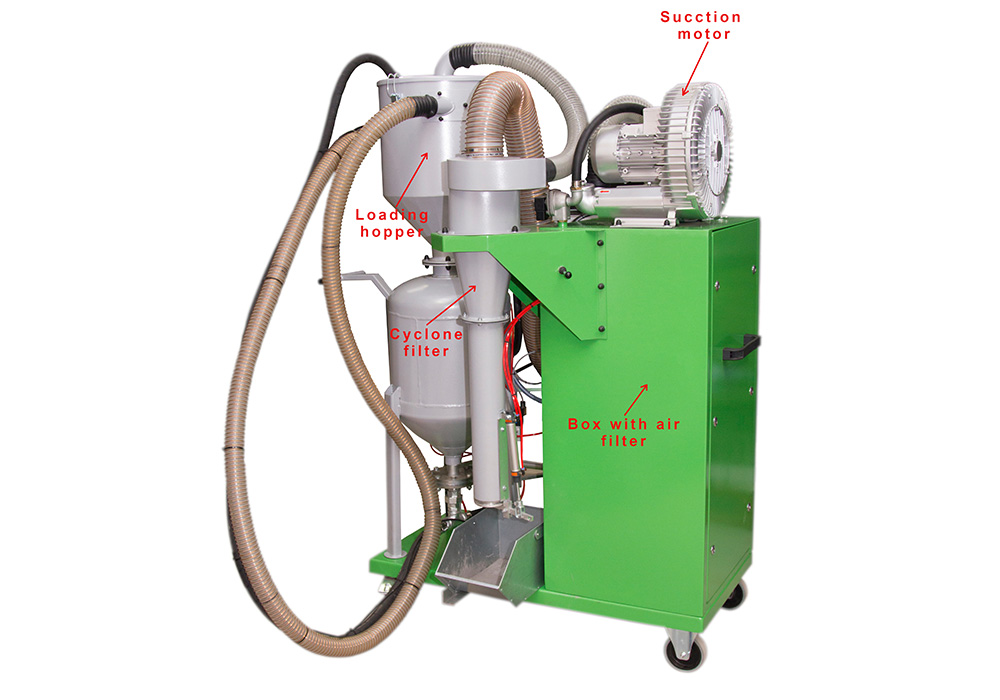
It is important to note that this three-stage, closed-circulation system is a feature exclusive to the SB Orkan Plus and SB Eol Plus dustless sandblasters, both of which are also dedicated for use with the CNC Akwilon system. In contrast, the SB Plus and SB Zephyr models are equipped with a two-stage separation and abrasive recovery system, as they do not include a cyclone filter.
The Closed-Circulation Advantage
This entire process operates continuously within a closed-circulation system. Your abrasive is consistently recovered for reuse, while dust and debris are efficiently channelled into the cyclone’s collection bin and the dust box drawer.
The Importance of Quality Abrasives
This efficient recovery system makes investing in higher-quality, more durable abrasives a sound economic decision. The right hardness and particle size will ensure longevity, leading to significant savings in both time and material costs. You’ll find you’re much more inclined to use premium abrasive media when you know it’s being effectively recycled.
Benefits – Cleanliness, Safety, and Efficiency
The result is a remarkably clean and safe working environment. Dust is only encountered when emptying the cyclone bin and dust drawer. For the operator, standard Personal Protective Equipment (PPE) such as safety goggles, gloves, and ear defenders is typically sufficient, a stark contrast to the full-body suits and respiratory helmets often required for traditional dry blasting. This not only enhances operator comfort but also significantly reduces health risks associated with airborne silica and other harmful particles.
Wouldn’t you agree this is a more sensible and advantageous approach to surface preparation? We’d be keen to hear your thoughts – please get in touch!